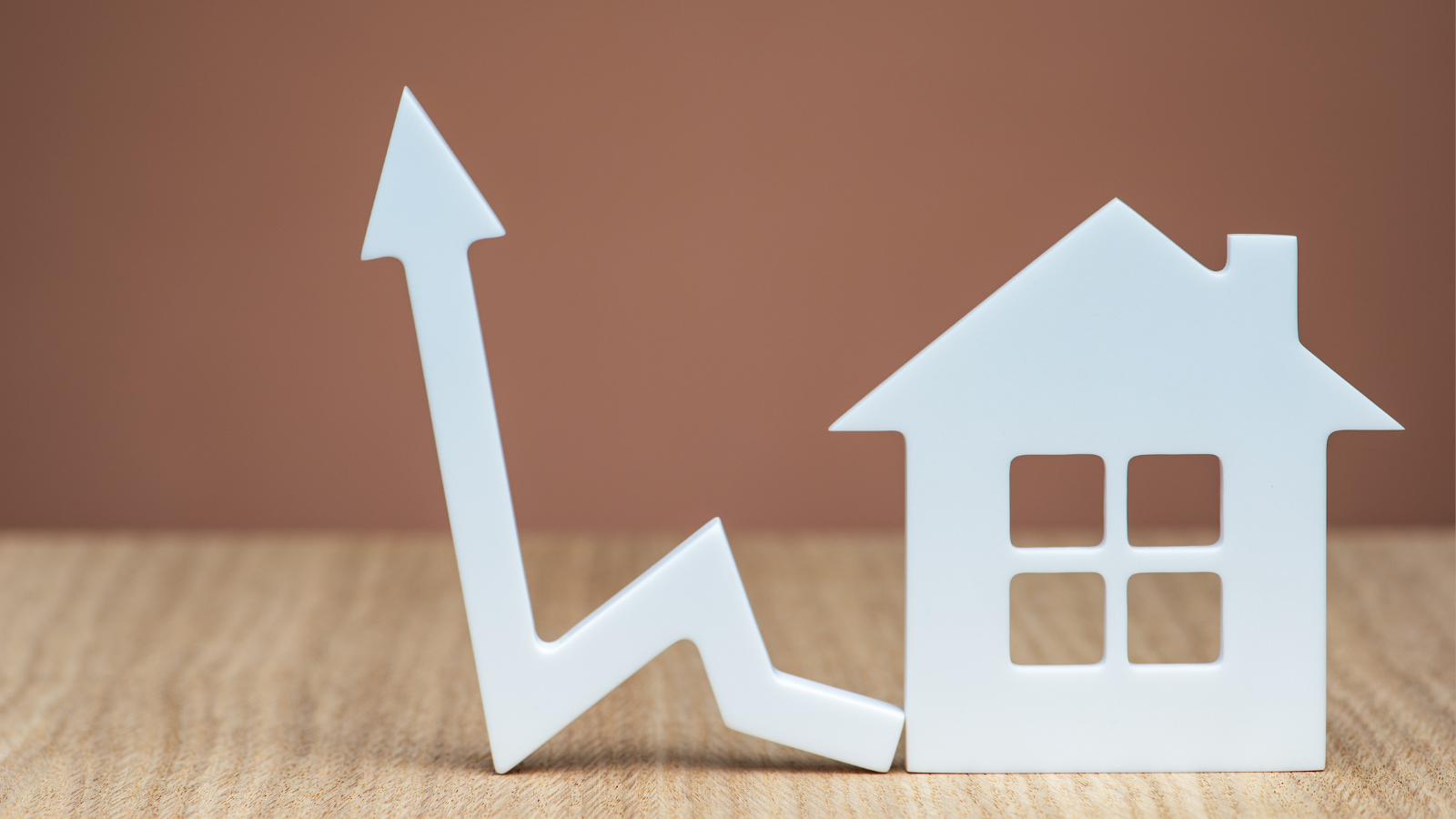
Soaring home prices and escalating rent, compounded by a pervasive housing shortage, mean affordable living has become increasingly elusive to many Canadians.
Median after-tax income data from Statistics Canada and house prices data from the Canadian Real Estate Association (CREA) reveal that there has been a significant surge in the average home price-to-income ratio, escalating from 4.1 in 2005 to 9.8 in 2022. Concurrently, the annual change in rental prices hit a record peak of 8% in 2023, outpacing annual inflation and wage growth at 3.1% and 4.8%, respectively. These dynamics have resulted in a historically low vacancy rate of 1.5%, the lowest rate ever recorded by the Canada Mortgage and Housing Corporation (CMHC), underscoring the increasingly challenging Canadian housing market.
Canada’s housing challenge has complex roots. Analyses have pointed to construction labour shortages, immigration and demand for housing, and the financialization of the housing market as potential causes of today’s crisis. Housing technology could be one important tool in what will need to be a multifaceted solution.
Federal Interventions to Canada’s Housing Crisis
On April 12th, the government announced a comprehensive initiative called Solving the Housing Crisis: Canada’s Housing Plan. This plan aims to make renting and homeownership more economical by increasing the number of homes nationwide. The government plans to add a minimum of 2 million net new homes in addition to the 1.87 million homes already projected to be built—resulting in a total of 3.87 million homes by 2031. Further, the 2024 federal budget has earmarked $15 billion in funding for the Apartment Construction Loan Program and a $6 billion housing infrastructure fund for communities, allowing for the construction of fourplex developments instead of single-family homes.
Notably, the federal government also aims to spur innovation within the construction industry through the investment of $600 million in research and development of advanced housing technologies such as prefabricated housing, mass timber, panelization, 3D printing applications and the creation of catalogues featuring pre-approved home designs.
In this article, we answer the question: What innovative housing technologies is Canada investing in, and how might they impact the housing market?
What is Housing Technology?
Traditional building techniques were labour-intensive and primarily used wood. The introduction of mass-produced nails and power-sawn lumber in the early to mid-1900s revolutionized the industry, enabling more efficient methods like stud framing.
Today, construction relies on materials like concrete and steel, focusing on sustainability and energy efficiency. In addition to these changes, builders now leverage techniques where parts or entire building sections are constructed offsite and assembled at the final site. These methods enhance efficiency, reduce costs, and improve quality control. However, despite these advancements, the industry faces labour shortages, high costs, low productivity, and a lack of automation. Furthermore, paper-based internal processes and lengthy application procedures for permit approvals often lead to long wait times.
These inefficiencies highlight the need for the increased use of advanced technology to achieve maximum efficiency, cost savings, and improved time management, resulting in a more efficient and sustainable future for the industry.
Emerging Housing Technologies
Panelization
Panelization is a process where walls, floors, and ceilings are designed using computer software, offering increased accuracy and reduced labour and waste. The panels are constructed in a climate-controlled factory and then delivered to the site for assembly. This method allows for prefabrication and storage of panels until needed and allows for quicker installation, reducing the time and cost of going from foundation to sealed building.
Successes: The Structural Building Components Association (SBCA) conducted an experiment comparing panelization with traditional methods. They built two identical homes side-by-side, one using panelization and the other using traditional methods. The panelized house required 63% fewer hours, produced 76% less waste, and was 16% cheaper to build.
Drawbacks: Panels can be damaged during transportation to the construction site and incur transportation fees, which can become costly depending on how far the site is from the plant. While there are time savings from not building components on site, construction companies must allocate more hours to coordinate with the panelization company to review designs, schedule deliveries, and facilitate delivery with trucking companies.
3D Printing
3D printing makes three-dimensional objects from digital files. In construction, mortar or concrete is fed into a 3D printer, whereafter automated robotic arms travel around the foundation of a site and lay down successive layers of mortar/concrete, each layer stacking on top of each other until the desired structure is complete.
Successes: Nidus3D, based in Kingston, Ontario, in collaboration with the Canada Mortgage and Housing Corporation (CMHC) and the University of Windsor, built Canada’s first 3D-printed multi-unit homes in Leamington, Ontario. Nidus3D also went on to build North America’s first 3D-printed three-story residential building, where printing was completed in less than a month and used less material than traditional methods would have required. These cost and time savings are backed up by industry stakeholders such as 3drific, which asserts that 3D printing can reduce construction costs by 20-40% and reduce design time by 60%.
Drawbacks: High capital costs include the printer itself, which can cost hundreds of thousands of dollars, in addition to electricity and maintenance. In terms of skills required, the construction industry’s labour shortage is exacerbated by the need for 3D design and operation skills. While 3D printers can create building structures, the rough appearance of 3D-printed walls needs post-processing and finishing, which requires traditional trades. When considering these factors, the actual savings are often less than expected.
Mass Timber
Mass timber is an engineered, wood-based structural building material suitable for large-scale construction projects. It is as strong and safe as alternative building materials but faster and easier to build with. If substituted for concrete and steel, mass timber would cut building emissions by as much as 25%.
Successes: Forest industry company StoraEnso found that, because of the high degree of prefabrication involved in producing mass timber, 50-70% fewer labourers were needed, and, due to timber's lightweight nature, 80% fewer deliveries were required. Additionally, the market value of mass timber is comparable to that of concrete but offers 30% faster construction times.
Drawbacks: Despite the apparent benefits of mass timber, it only accounts for about 1% of all building construction materials used in Canada in 2022. Reasons for the low uptake include building codes limiting construction and higher insurance premiums for mass timber buildings (the Southeast Concrete Masonry Association suggests this is not because it is more dangerous but because it is still new and not well established in the industry). There is also a mismatch in demand and supply where most producers of mass timber are in British Columbia, while most of the demand is in Eastern Canada, which can drive up shipping costs.
Building Information Modeling (BIM)
BIM is a digital process that facilitates collaboration and management of digital models of buildings from design through to construction and maintenance. It creates 3D models (digital twins) and shares accurate information about materials, measurements, and performance metrics, which prevents supply chain issues. Benefits include improved communication and decision-making, enhanced designs, and the availability of high-quality information, which reduces risks.
Successes: The Celsius Project in Sweden was completed in November 2020 and highlighted the benefits of Total BIM implementation. In this initiative, BIM was used as the single source of information throughout all project phases in constructing a six-floor, 12,000 m² office building. The design process was estimated to be 10% faster and 80% more accurate than traditional methods, which would have involved using 2D drawings. This led to the project being completed on time and under budget despite unexpected costs occurring during the project cycle.
Drawbacks: BIM has become increasingly popular in Canada but requires a significant upfront investment in software and training, and its full benefits are only realized when all parties involved in the construction process use it. While governments around the globe have initiated programs to mandate or at least incentivize the use of BIM in construction projects, Canada has no such initiative in place, which leaves the country lagging in adoption rates. In addition to the lack of federal support, research by buildingSMART Canada and the National Research Council of Canada outlined the challenges industry players face in implementing BIM technology. The main barriers include a lack of awareness and understanding of BIM, insufficient training and education on BIM, resistance to change from traditional workflows, and a lack of standardization across stakeholders, which makes coordination difficult.
Augmented Reality
Augmented Reality (AR) involves integrating real-life objects with computer-generated images, while Virtual Reality (VR) simulates an entire environment or scenario. These technologies, coupled with hardware such as smart helmets, glasses, or smartphones, can create immersive 3D experiences, allowing stakeholders to interact with a building before actual construction. This facilitates instant feedback during early-stage development, accelerating project lifecycles and ensuring that budgets are met.
Successes: US company Layton Construction reported a 90% reduction in pre-construction costs due to using VR instead of physical mock-ups during the design phase of their project. Besides quality assurance and error detection, VR and AR can help bridge the skills gap by facilitating remote machinery operations where off-site personnel can staff construction projects, and this technology can be leveraged to increase the skilled workforce by training workers in a virtually risk-free environment. According to PricewaterhouseCoopers’ study on the effectiveness of VR, participants completed training four times faster than classroom training and were twice as confident to apply their skills after training.
Drawbacks: The prohibitive cost of VR and AR equipment, the potential need for significant changes to existing workflows, and a lack of qualified personnel to utilize these technologies effectively are major limitations to their widespread implementation.
Conclusion
Advancements in building materials, techniques, and processes are often slow to be adopted within the construction industry due to insufficient funding and builders’ tendency to resist integrating technological progress into their procedures unless the benefits are well-documented and proven.
Despite this, Canada is pushing to promote investment in technologies and approaches that could lead to significant productivity gains. The increased use of technology combined with progressive urban planning and zoning policy could be one way to help Canada's construction sector meet the growing demand for living space.
Sheldon Lopez is an Economist and Research Analyst at ICTC.